ការបោះពុម្ពទឹកថ្នាំកាំរស្មី UV ជាធម្មតាប្រកាន់ខ្ជាប់នូវវិធីសាស្រ្តនៃការសម្ងួតកាំរស្មីយូវីភ្លាមៗ ដូច្នេះទឹកថ្នាំអាចប្រកាន់ខ្ជាប់យ៉ាងរហ័សទៅនឹងផ្ទៃនៃវត្ថុធាតុស្អិតដោយខ្លួនឯងនៃខ្សែភាពយន្ត។ ទោះបីជាយ៉ាងណាក៏ដោយ នៅក្នុងដំណើរការនៃការបោះពុម្ព បញ្ហានៃការស្អិតជាប់មិនល្អនៃទឹកថ្នាំកាំរស្មី UV ទៅលើផ្ទៃនៃវត្ថុធាតុដេលចាប់តាមខ្លួនរបស់ខ្សែភាពយន្តតែងតែកើតឡើង។
តើការស្អិតរបស់ទឹកថ្នាំ UV គឺជាអ្វី?
ស្ថានីយផ្សេងគ្នាមានវិធីសាស្រ្តផ្សេងគ្នាសម្រាប់ការធ្វើតេស្តភាពស្អិតរបស់ទឹកថ្នាំ UV ។ ទោះជាយ៉ាងណាក៏ដោយ នៅក្នុងឧស្សាហកម្មស្លាកសញ្ញាដោយខ្លួនឯង អតិថិជនភាគច្រើននឹងប្រើកាសែត 3M 810 ឬ 3M 610 សម្រាប់ការធ្វើតេស្តភាពស្អិតរបស់ទឹកថ្នាំ។
លក្ខណៈវិនិច្ឆ័យវាយតម្លៃ៖ ភាពរឹងមាំនៃទឹកថ្នាំត្រូវបានវាយតម្លៃទៅតាមចំនួនទឹកថ្នាំដែលជាប់គាំង បន្ទាប់ពីកាសែត adhesive ត្រូវបានជាប់គាំងលើផ្ទៃផ្លាក បន្ទាប់មកយកចេញ។
កម្រិតទី១៖ គ្មានទឹកថ្នាំធ្លាក់ចេញទេ។
កម្រិតទី 2៖ ទឹកថ្នាំធ្លាក់បន្តិច (<10%)
កម្រិតទី 3៖ ការស្រក់ទឹកថ្នាំកម្រិតមធ្យម (10% ~ 30%)
កម្រិតទី 4៖ ការស្រក់ទឹកថ្នាំធ្ងន់ធ្ងរ (30% ~ 60%)
កម្រិតទី 5៖ ទឹកថ្នាំស្ទើរតែទាំងអស់ធ្លាក់ចុះ (> 60%)
សំណួរទី 1:
នៅក្នុងការផលិត យើងតែងតែជួបប្រទះនឹងបញ្ហាដែលថានៅពេលដែលវត្ថុធាតុមួយចំនួនត្រូវបានបោះពុម្ពជាធម្មតា ភាពស្អិតរបស់ទឹកថ្នាំគឺយល់ព្រម ប៉ុន្តែបន្ទាប់ពីល្បឿនបោះពុម្ពត្រូវបានកែលម្អ ការស្អិតរបស់ទឹកថ្នាំកាន់តែអាក្រក់ទៅៗ។
មូលហេតុ 1:
នៅពេលដែល photoinitiator នៅក្នុងទឹកថ្នាំ UV ស្រូបយកពន្លឺ UV ដើម្បីបង្កើតរ៉ាឌីកាល់សេរី វានឹងឆ្លងកាត់តំណភ្ជាប់ជាមួយ monomer prepolymer នៅក្នុងសមាសធាតុទឹកថ្នាំដើម្បីបង្កើតរចនាសម្ព័ន្ធបណ្តាញ ដែលជាដំណើរការបណ្តោះអាសន្នពីរាវទៅរឹង។ ទោះជាយ៉ាងណាក៏ដោយ នៅក្នុងការបោះពុម្ពជាក់ស្តែង ទោះបីជាផ្ទៃទឹកថ្នាំស្ងួតភ្លាមៗក៏ដោយ ក៏វាពិបាកសម្រាប់ពន្លឺអ៊ុលត្រាវីយូឡេក្នុងការជ្រាបចូលទៅក្នុងស្រទាប់ផ្ទៃទឹកថ្នាំដែលរឹងដើម្បីទៅដល់ស្រទាប់ខាងក្រោម ដែលបណ្តាលឱ្យមានប្រតិកម្មគីមីនៃទឹកថ្នាំស្រទាប់ខាងក្រោមមិនពេញលេញ។
ការណែនាំ៖សម្រាប់ការបោះពុម្ពទឹកថ្នាំជ្រៅ និងការបោះពុម្ពស្រាល ទឹកថ្នាំដែលមានកម្លាំងពណ៌ខ្ពស់អាចត្រូវបានប្រើដើម្បីកាត់បន្ថយកម្រាស់នៃស្រទាប់ទឹកថ្នាំ ដែលមិនត្រឹមតែអាចធានាបាននូវភាពស្ងួតនៃទឹកថ្នាំតែមួយស្រទាប់ប៉ុណ្ណោះទេ ប៉ុន្តែថែមទាំងបង្កើនប្រសិទ្ធភាពផលិតកម្មផងដែរ។
មូលហេតុ 2:
ចង្កៀង UV mercury ជាទូទៅប្រើបានប្រហែល 1000 ម៉ោង ហើយវាអាចភ្លឺបានបន្ទាប់ពីចង្កៀង UV ប្រើលើសពី 1000 ម៉ោង ប៉ុន្តែទឹកថ្នាំ UV មិនអាចស្ងួតទាំងស្រុងបានទេ។ ជាការពិតនៅពេលដែលចង្កៀងកាំរស្មី UV បានឈានដល់អាយុកាលសេវាកម្មរបស់វា ខ្សែកោងវិសាលគមរបស់វាត្រូវបានផ្លាស់ប្តូរ។ ពន្លឺអ៊ុលត្រាវីយូឡេដែលបញ្ចេញមិនឆ្លើយតបនឹងតម្រូវការនៃទឹកថ្នាំស្ងួត ហើយថាមពលអ៊ីនហ្វ្រារ៉េដបានកើនឡើង ដែលបណ្តាលឱ្យខូចទ្រង់ទ្រាយសម្ភារៈ និងស្នាមប្រេះដោយសារសីតុណ្ហភាពខ្ពស់។
ការណែនាំ៖ពេលវេលាប្រើប្រាស់នៃចង្កៀងកាំរស្មី UV គួរតែត្រូវបានកត់ត្រាឱ្យបានត្រឹមត្រូវ និងជំនួសឱ្យទាន់ពេលវេលា។ ក្នុងអំឡុងពេលផលិតកម្មធម្មតា វាក៏ចាំបាច់ផងដែរក្នុងការត្រួតពិនិត្យភាពស្អាតនៃចង្កៀងកាំរស្មី UV និងសម្អាតឧបករណ៍ឆ្លុះបញ្ចាំង។ ជាទូទៅមានតែ 1/3 នៃថាមពលរបស់ចង្កៀងកាំរស្មី UV ដោយផ្ទាល់ទៅលើផ្ទៃសម្ភារៈ ហើយ 2/3 នៃថាមពលត្រូវបានឆ្លុះបញ្ចាំងដោយឧបករណ៍ឆ្លុះបញ្ចាំង។
សំណួរទី 2:
នៅក្នុងការផលិត យើងតែងតែជួបប្រទះនឹងបញ្ហាដែលថានៅពេលដែលវត្ថុធាតុមួយចំនួនត្រូវបានបោះពុម្ពជាធម្មតា ភាពស្អិតរបស់ទឹកថ្នាំគឺយល់ព្រម ប៉ុន្តែបន្ទាប់ពីល្បឿនបោះពុម្ពត្រូវបានកែលម្អ ការស្អិតរបស់ទឹកថ្នាំកាន់តែអាក្រក់ទៅៗ។
មូលហេតុទី 1:
ពេលវេលាទំនាក់ទំនងខ្លីរវាងទឹកថ្នាំ និងស្រទាប់ខាងក្រោមនាំឱ្យទំនាក់ទំនងកម្រិតម៉ូលេគុលមិនគ្រប់គ្រាន់រវាងភាគល្អិត ដែលប៉ះពាល់ដល់ការស្អិត។
ភាគល្អិតនៃទឹកថ្នាំ និងស្រទាប់ខាងក្រោមសាយភាយ ហើយភ្ជាប់គ្នាទៅវិញទៅមកដើម្បីបង្កើតជាទំនាក់ទំនងកម្រិតម៉ូលេគុល។ តាមរយៈការបង្កើនពេលវេលាទំនាក់ទំនងរវាងទឹកថ្នាំ និងស្រទាប់ខាងក្រោមមុនពេលស្ងួត ឥទ្ធិពលនៃការតភ្ជាប់រវាងម៉ូលេគុលអាចមានសារៈសំខាន់ជាងមុន ដូច្នេះហើយការបង្កើនភាពស្អិតរបស់ទឹកថ្នាំ។
សំណូមពរ៖ បន្ថយល្បឿនបោះពុម្ព ធ្វើឱ្យទឹកថ្នាំមានទំនាក់ទំនងពេញលេញជាមួយស្រទាប់ខាងក្រោម និងធ្វើឱ្យការស្អិតរបស់ទឹកថ្នាំប្រសើរឡើង។
មូលហេតុទី ២៖
ពេលវេលាប៉ះពាល់នឹងពន្លឺកាំរស្មីយូវីមិនគ្រប់គ្រាន់ បណ្តាលឱ្យទឹកថ្នាំមិនស្ងួតទាំងស្រុង ប៉ះពាល់ដល់ការស្អិត
ការកើនឡើងនៃល្បឿនបោះពុម្ពក៏នឹងកាត់បន្ថយពេលវេលា irradiation នៃពន្លឺ UV ដែលនឹងកាត់បន្ថយថាមពលដែលចាំងលើទឹកថ្នាំ ដូច្នេះប៉ះពាល់ដល់ស្ថានភាពស្ងួតរបស់ទឹកថ្នាំ ដែលបណ្តាលឱ្យមានភាពស្អិតជាប់មិនល្អដោយសារតែការស្ងួតមិនពេញលេញ។
ការណែនាំ៖បន្ថយល្បឿននៃការបោះពុម្ព ទុកឱ្យទឹកថ្នាំស្ងួតទាំងស្រុងនៅក្រោមពន្លឺកាំរស្មី UV និងធ្វើឱ្យការស្អិតជាប់កាន់តែប្រសើរឡើង។
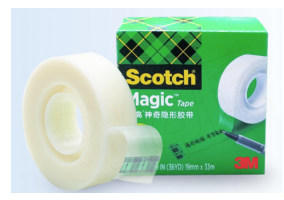
ពេលវេលាបង្ហោះ៖ ថ្ងៃទី 09-09-2022